The Basic Principles Of Alcast Company
The Basic Principles Of Alcast Company
Blog Article
An Unbiased View of Alcast Company
Table of ContentsAlcast Company Things To Know Before You Get ThisThe Best Guide To Alcast CompanyGetting The Alcast Company To WorkThe Single Strategy To Use For Alcast CompanyOur Alcast Company DiariesThe Definitive Guide to Alcast Company
The subtle difference hinges on the chemical material. Chemical Contrast of Cast Aluminum Alloys Silicon advertises castability by reducing the alloy's melting temperature and enhancing fluidness during casting. It plays an important duty in allowing elaborate mold and mildews to be filled precisely. Furthermore, silicon adds to the alloy's strength and wear resistance, making it important in applications where longevity is crucial, such as auto components and engine parts.It additionally boosts the machinability of the alloy, making it less complicated to refine into completed products. In this means, iron contributes to the overall workability of aluminum alloys. Copper raises electric conductivity, making it beneficial in electric applications. It likewise enhances corrosion resistance and contributes to the alloy's general strength.
Manganese contributes to the strength of light weight aluminum alloys and enhances workability. Magnesium is a light-weight element that offers toughness and effect resistance to aluminum alloys.
See This Report about Alcast Company
It permits the production of lightweight elements with exceptional mechanical homes. Zinc boosts the castability of light weight aluminum alloys and helps control the solidification procedure during casting. It enhances the alloy's strength and firmness. It is usually found in applications where intricate shapes and great information are necessary, such as ornamental spreadings and particular auto components.

The main thermal conductivity, tensile toughness, return strength, and prolongation vary. Select suitable raw materials according to the performance of the target product created. Among the above alloys, A356 has the highest thermal conductivity, and A380 and ADC12 have the most affordable. The tensile limit is the contrary. A360 has the very best return stamina and the greatest prolongation price.
The Facts About Alcast Company Revealed
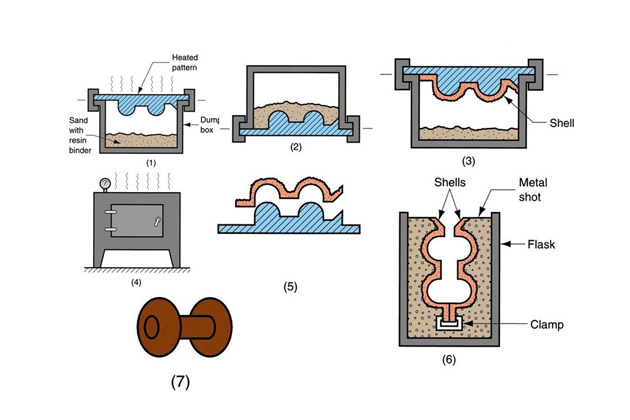
In accuracy spreading, 6063 is well-suited for applications where intricate geometries and top quality surface coatings are paramount. Examples consist of telecommunication units, where the alloy's remarkable formability permits smooth and cosmetically pleasing layouts while maintaining architectural honesty. In the Illumination Solutions sector, precision-cast 6063 components produce sophisticated and efficient lighting components that call for intricate shapes and great thermal efficiency.
The A360 displays exceptional elongation, making it perfect for complex and thin-walled components. In precision casting applications, A360 is well-suited for industries such as Customer Electronic Devices, Telecommunication, and Power Devices.
Rumored Buzz on Alcast Company
Its one-of-a-kind residential properties make A360 a valuable selection for accuracy spreading in these markets, boosting item toughness and high quality. Light weight aluminum alloy 380, or A380, is an extensively used spreading alloy with numerous distinctive attributes. It uses outstanding castability, making it an excellent choice for precision spreading. A380 exhibits good fluidity when molten, making sure elaborate and thorough molds are accurately recreated.
In precision spreading, light weight aluminum 413 radiates in the Customer Electronics and Power Devices markets. This alloy's exceptional deterioration resistance makes it a superb option for exterior applications, making sure resilient, durable items in the discussed industries.
Excitement About Alcast Company
When you have actually decided that the light weight aluminum pass away casting process is suitable for your project, a crucial next action is selecting one of the most ideal alloy. The aluminum alloy you select will significantly impact both the spreading procedure and the homes of the end product. As a result of this, you need to make your choice thoroughly and take an educated strategy.
Figuring out the most ideal aluminum alloy for your application will indicate considering a large range of characteristics. The initial group addresses alloy attributes that impact the manufacturing procedure.
The Only Guide to Alcast Company
The alloy you select for die spreading directly influences several aspects of the casting procedure, like exactly how very easy the alloy is to collaborate with and if it is vulnerable to casting problems. Warm breaking, additionally referred to as solidification cracking, is a normal die spreading flaw for light weight aluminum alloys that can result in interior or surface-level rips or fractures.
Particular aluminum alloys are much more at risk to hot fracturing than others, and your selection ought to consider this. Another typical flaw located in the die casting of light weight aluminum is die soldering, which is when the cast stays with the die walls and makes ejection difficult. It can damage both the actors and the die, so you need to look for alloys with high anti-soldering homes.
Corrosion resistance, which is already a remarkable attribute of aluminum, can vary substantially from alloy to alloy and is a vital characteristic to think about depending upon the ecological problems your item will be revealed to (aluminum casting company). Use resistance is one more building generally sought in aluminum products and can set apart some alloys
Report this page